Finest Practices for Preventing Weld Undercut: Grasping the Basics
Mastering the Art of Welding: Exactly How to Prevent Undercut Welding Issues for Flawless Construction Outcomes
By comprehending the origin creates of undercut welding and carrying out reliable techniques to stop it, welders can elevate their craft to new levels of excellence. In the quest of flawless fabrication outcomes, mastering the art of welding to prevent undercut issues is not simply a skill yet a necessity for those making every effort for perfection in their job.
Recognizing Undercut Welding
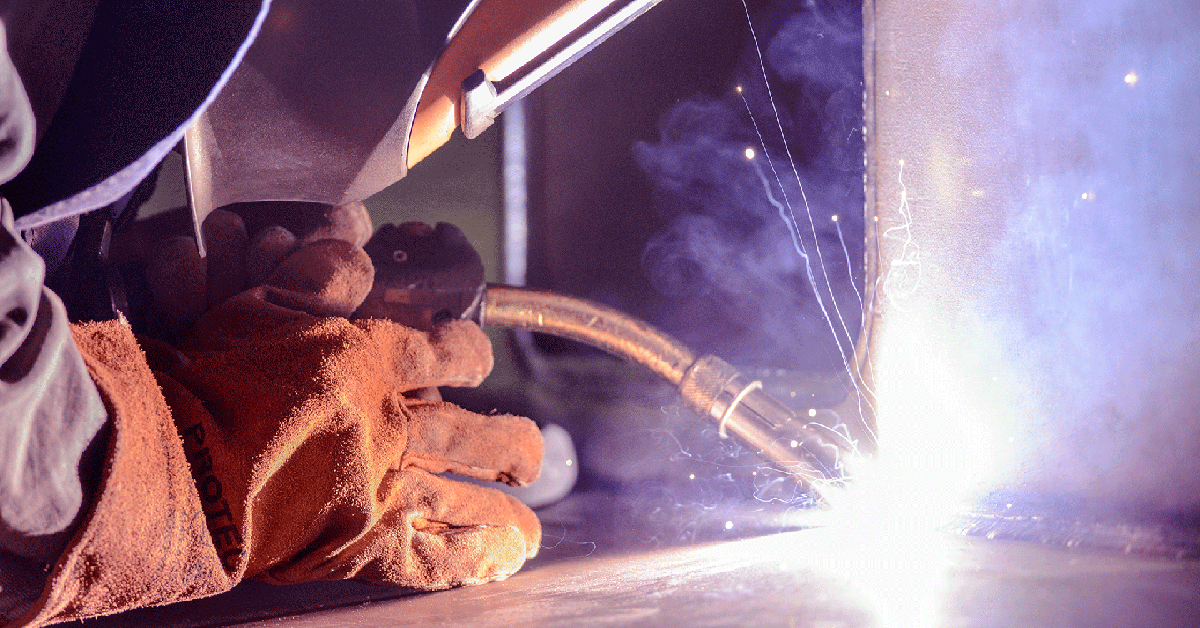
To prevent undercut welding, welders should make certain proper welding parameters, such as changing the current, voltage, traveling rate, and keeping the right electrode angle. By recognizing the causes of undercut welding and executing precautionary procedures, welders can attain high-quality, structurally sound welds.
Root Causes Of Undercut in Welding
Recognizing the aspects that contribute to undercut in welding is essential for welders to create top quality, structurally sound welds. When the weld steel does not effectively fill the groove formed in between the base steel and the previously transferred weld metal, undercutting takes place. Several aspects can bring about undercut in welding. One typical reason is too much heat input. Welding at heats for extended durations can cause the base metal thawing even more than preferred, causing undercut. Insufficient welding incorrect or current welding rate can also contribute to damage. Inadequate current might not give sufficient warmth to melt the base and filler steels effectively, while excessive speed can prevent correct blend, triggering undercut. Additionally, inappropriate electrode angles or wrong lantern control strategies can create locations of low weld steel deposition, promoting undercut. Recognizing these reasons and implementing correct welding strategies can assist avoid undercutting issues, making sure resilient and strong welds.
Strategies to Avoid Undercutting

To alleviate the risk of damaging in welding, welders can use critical welding techniques intended at boosting the top quality and stability of the weld joints. Additionally, utilizing the proper welding technique for the specific joint arrangement, such as weave or stringer grains, can contribute to decreasing undercutting.
Utilizing back-step welding techniques and controlling the weld grain account can also help distribute heat evenly and reduce the threat of undercut. their website Routine inspection of the weld joint during and after welding, as well as implementing high quality look at these guys assurance procedures, can assist in addressing and detecting undercutting concerns quickly.
Significance of Proper Welding Parameters
Selecting and maintaining suitable welding parameters is vital for accomplishing successful welds with minimal issues. Welding specifications describe variables such as voltage, current, take a trip rate, electrode angle, and shielding gas flow rate that straight affect the welding procedure. These criteria must be meticulously changed based on the kind of product being bonded, its density, and the welding strategy utilized.
Proper welding parameters make sure the best quantity of warm is related to thaw the base steels and filler material uniformly. If the parameters are set too expensive, it can cause excessive heat input, causing spatter, burn-through, or distortion. On the various other hand, if the specifications are too low, incomplete fusion, lack of penetration, or damaging may occur.
High Quality Guarantee in Welding Operations
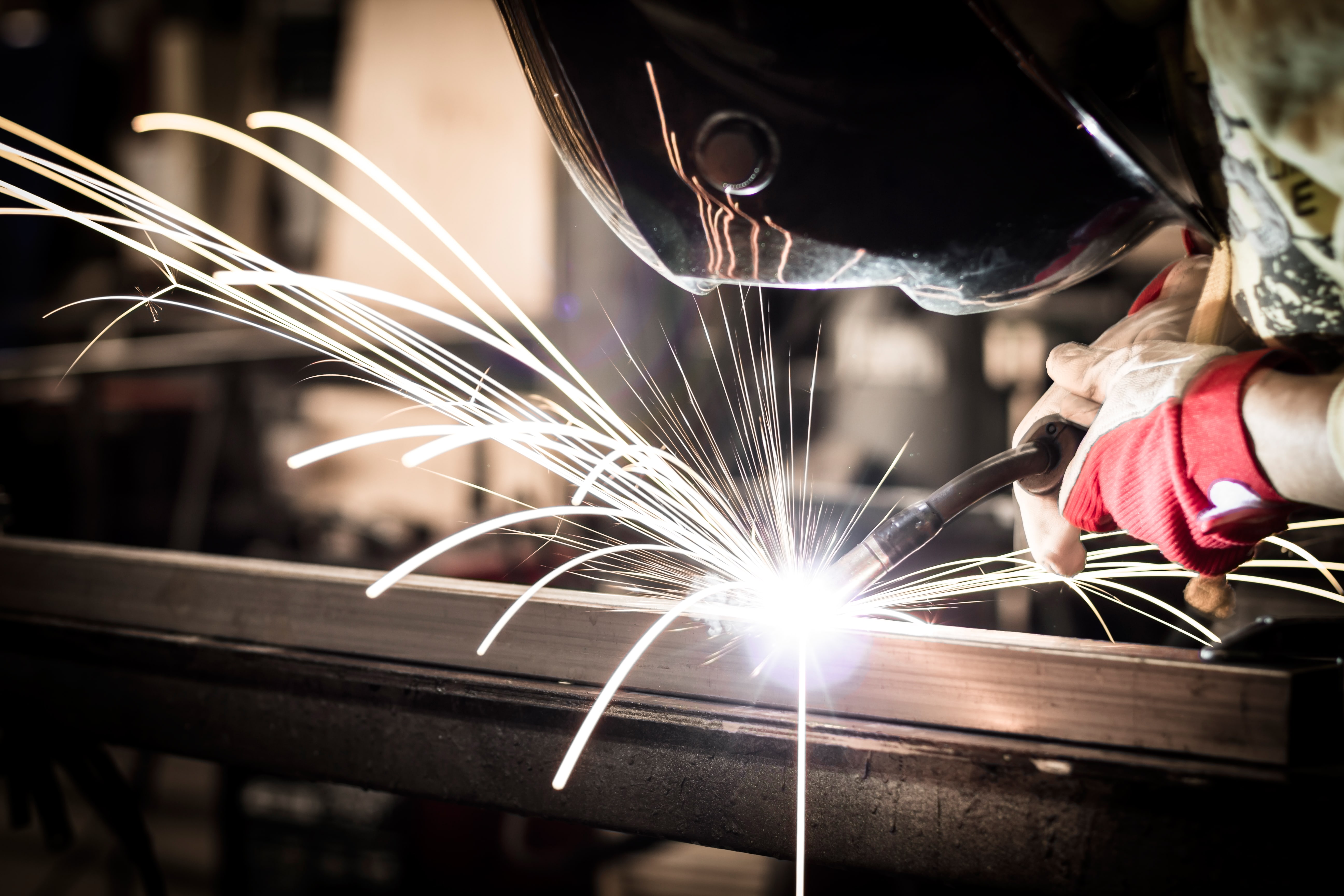
Verdict
In final thought, grasping the art of welding needs a complete understanding of undercut welding, its causes, and methods to avoid it. By ensuring correct welding parameters and applying quality assurance methods, flawless fabrication outcomes can be achieved. It is important for welders to regularly pursue quality in their welding procedures to avoid undercut issues and generate premium welds.
Undercut welding, a common problem in welding processes, takes place when the weld steel doesn't appropriately fill up the groove and leaves a groove or clinical depression along the bonded joint.To stop undercut welding, welders need to make certain proper welding criteria, such as changing the current, voltage, traveling speed, and maintaining the right electrode angle. Poor welding current or inaccurate welding rate can likewise contribute to damage.To minimize the danger of undercutting in read the full info here welding, welders can use strategic welding methods intended at boosting the top quality and integrity of the weld joints.In final thought, grasping the art of welding needs a complete understanding of undercut welding, its reasons, and strategies to stop it.